How Technology Is Reshaping Traditional Manufacturing
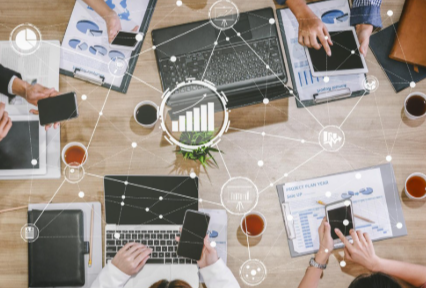
Technological advancements are fundamentally altering the landscape of traditional manufacturing. Automation streamlines production, while artificial intelligence optimizes processes. The integration of the Internet of Things facilitates real-time monitoring and data analysis, enhancing operational efficiency. As these innovations reshape workflows, they also redefine workforce requirements, emphasizing the need for new skills. This evolution raises questions about sustainability and consumer expectations. What implications do these changes hold for the future of manufacturing?
The Rise of Automation in Manufacturing
The surge of automation in manufacturing is fundamentally transforming production processes across various industries.
Robotic integration enhances efficiency and precision, leading to significant workforce transformation. As manual tasks diminish, workers are required to adapt to new roles that leverage technology.
This evolution not only fosters innovation but also emphasizes the need for continuous learning, ultimately empowering individuals to embrace a more autonomous and skilled future in manufacturing.
Harnessing Artificial Intelligence for Improved Processes
As manufacturers increasingly integrate artificial intelligence (AI) into their operations, they unlock unprecedented opportunities for process optimization and decision-making.
AI enhances predictive maintenance protocols, reducing equipment downtime and maintenance costs. Furthermore, it improves quality control by analyzing production data in real-time, enabling timely interventions.
This integration not only elevates operational efficiency but also fosters a culture of continuous improvement and innovation within manufacturing environments.
Read more: The Role of Artificial Intelligence in Data Management
The Role of the Internet of Things in Smart Manufacturing
While traditional manufacturing processes often relied on isolated systems, the Internet of Things (IoT) is transforming the landscape into a highly interconnected ecosystem.
Connected devices facilitate real-time communication and monitoring, enabling manufacturers to harness data analytics for informed decision-making.
This integration enhances operational efficiency, reduces downtime, and fosters innovation, with QR codes playing a key role in streamlining tracking and communication—ultimately empowering manufacturers to adapt swiftly to market dynamics and consumer demands.
Sustainability and Efficiency: The New Manufacturing Paradigm
Emphasizing sustainability and efficiency has become essential for modern manufacturing, especially as industries face increasing pressure to reduce their environmental impact.
By integrating renewable resources and innovative technologies, manufacturers can achieve significant waste reduction.
This new paradigm not only enhances operational efficiency but also aligns with consumer expectations for responsible production, ultimately fostering a manufacturing landscape that prioritizes both ecological integrity and economic viability.
Conclusion
In conclusion, the evolution of technology in manufacturing mirrors the Industrial Revolution’s transformative impact, heralding a new age of efficiency and innovation. Automation, artificial intelligence, and IoT are not merely tools; they are catalysts for a paradigm shift, redefining workforce dynamics and fostering sustainability. As manufacturers navigate this intricate landscape, they must embrace continuous learning and adaptability, ensuring their practices not only meet modern consumer expectations but also contribute positively to the global ecosystem.